Он рассказал, что уже сильно устал:
Заказов много, но выполнять не успевают и срывают сроки, обещанные клиентам. Постоянно то перед одним, то перед другим участком накапливается незавершенка. Виталию приходится «рулить» перекидыванием рабочих для тушения пожаров. Поэтому он уже забыл, что такое не только отпуск, но и выходные дни. Самый критичный участок — это станок по набивке труб наполнителем. На нем выполняется самая длительная и ответственная операция. Если заказ прошел этот станок, то экспедировать такой заказ уже легче и максимум через 3 дня он будет готов к отгрузке. Чтобы увеличить скорость производства в Китае заказали еще 2 набивочных станка. Но на момент курса по Теории ограничений они еще были в пути.
Случай с Виталием даже не был полноценным консалтинговым проектом. Это был короткий вводный курс по ТОС и несколько бесед. Мы разобрались, какой станок является ограничением его производственного потока и как надо изменить управление потоком с этим знанием. За пару недель Виталий увеличил количество выполняемых заказов в 3 раза. И разрешил себе уехать в отпуск.
Что было
Когда Виталий рассказал про свою ситуацию мы попросили показать сменно-суточные задания. Из них узнали, что рабочую бригаду постоянно срывают с участка набивочного станка на другие участки. И делает это сам Виталий. На этом станке из-за ответственности операции работали наиболее квалифицированные рабочие. Они, действительно, могли заменить многих и подтянуть производительность на других участках, но их на набивочном станке никто заменить не мог из-за недостатка квалификации. Причина перевода на другие участки — там по каким-то причинам скапливалось незавершенное производство, которое пугало Виталия.
Давайте разберемся с причинами появления «вспыхивающих» запасов незавершенного производства на разных участках. Я показала условный пример производственного потока на рисунке.
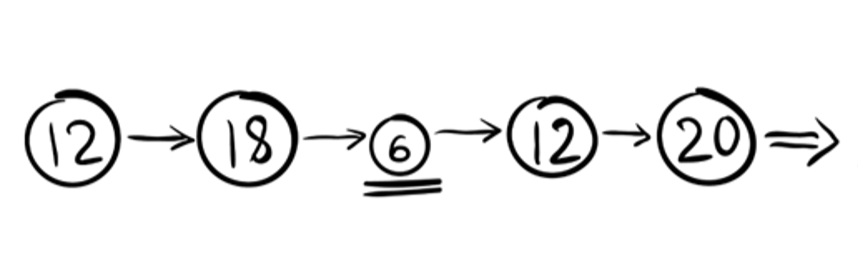
Чтобы получить готовый продукт нужно последовательно пройти через 5 станков и в кружках показано, сколько заготовок в час может обрабатывать каждый станок. Есть самый слабый ресурс, который может произвести не более 6 заготовок в час. 6 и будет максимальный выход (или максимальная скорость) всего потока при наилучших условиях. Хотя в реальности выпуск будет меньше 6: бывают поломки, брак, нестабильность сырья…
А спрос большой — рынок готов покупать 30 шт. продукции в час.
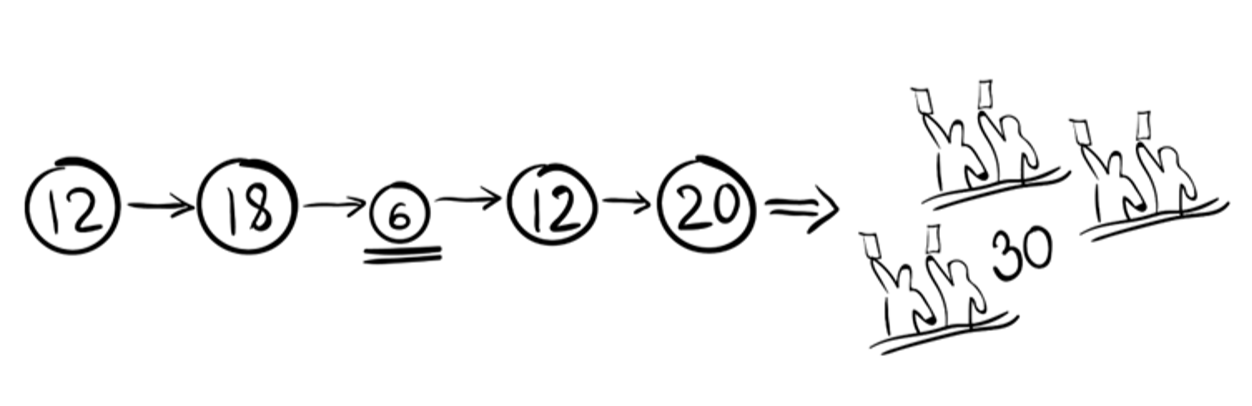
Если станки перед ограничением могут производить 12 и 18 ед в час, то понятно, как будет появляться незавершенка перед 3-им станком, который работает со скоростью в 2−3 раза ниже остальных. И, кстати, наличие большого объема незавершенки перед станком — один из признаков, что мы смотрим на ограничение мощности.
Но мы знаем из кейса про ТЭНы, что незавершенка скапливалась и на других станках. Как такое возможно? Возможно.
Представьте, что второй станок сломался и пару-тройку часов его чинили. Или у него очень длительная переналадка при переходе на другой тип продукции. За время простоя первый станок может «накидать» ему до 12 ед в час. Но это не повод беспокоиться. У второго станка избыточная мощность по сравнению со скоростью всего потока и он легко наверстает упущенное время.
А что будет если мы «дрогнем» и бросим на подмогу рабочих с третьего станка на второй? У третьего станка нет никакой избыточной мощности, чтобы наверстать упущенное время и это приведет к снижению выхода со всего потока. Т. е. мы выполним меньше заказов клиентов, меньше отгрузим, меньше заработаем и имеем риск потерять недовольных клиентов.
Что сделали?
1. Договорились об эксперименте. Как бы сильно ни хотелось — людей с этого участка не срываем. Даже если они по какой-то причине простаивают, то все равно сидят и ждут заготовок и хватаются за них, как «за горячие пирожки». Да, время этих высоко квалицированных рабочих ценно, но оно ценно только при работе на набивочном станке.
2. Составляем планы для станков до набивочного таким образом, чтобы ситуации «сидят и ждут» на набивочном были минимальными. Это интересная задачка, как рассчитывать технологические партии на станках с понимаем ограничения потока.
Два простых действия привели к тому, что скорость потока увеличилась в 2 раза. Так много времени теряли из-за простоев станка: «перекидывания» рабочих и отсутствия заготовок перед ограничением.
Но были еще причины потерь ценного времени этого станка.
Станок простаивал несколько минут в каждом цикле работы, пока рабочие надевали заклепки на одну сторону заготовки-трубы. Они подготавливали по несколько труб и устанавливали их в станок, после чего начиналась технологическая операция. Во время операции внимание рабочего было на станке и он не мог устанавливать заклепки на следующую партию труб. Но установка заклепок — это не космические технологии. Это могут делать и менее квалифицированные сотрудники. Так появилось решение 3.
3. Взяли дополнительный персонал на вспомогательную операцию установки заклепок на трубы. А рабочие сфокусировались только на тех.операции.
Это действие привело к дальнейшему росту производительности станка и выхода со всего потока.

Итого скорость работы станка выросла в 3 раза.
А пришедшие из Китая станки продали.

Выводы истории:
— Обычно люди внутри процесса знают, что является ограничением мощности (если такое у вас есть).
Часто возникает большое желание вытащить из ERP кучу данных, обложиться цифрами и рассчитать суперточно, что же там у нас происходит. Но на самом деле все проще — сходите в цех, поговорите с людьми, понаблюдайте за процессом. Есть секрет: если вы ошибетесь — вы быстро это поймете и это позволит найти реальное ограничение сильно быстрее и надежнее, чем данные из ERP, которые сложились такими из-за наших управленческих решений, а не архитектуры потока.
— Нельзя терять ни минуты ресурса с ограниченной мощностью.
Это звучит элементарно просто и вам будут рассказывать, что конечно же никто не теряет время этого ценного станка или сотрудника. Но понаблюдайте за работой, поговорите с рабочим и у вас будет много идей, как повысить производительность этого ценного ресурса. Часто обнаруживается, что теряется около 50% времени ограничения. Сама не перестаю удивляться, когда находим эти резервы, но реально так.
Прошло уже много лет с того курса. Полгода назад мы встречались с Виталием. Заказов стало сильно больше, а отпуска теперь регулярные.